Silk screen printing is a versatile and classic method for creating vibrant designs on various surfaces, including textiles like cotton ribbons. This technique involves transferring ink through a stencil (or screen) to produce striking visuals that stand out. Its origins date back thousands of years to China and Egypt, yet it remains incredibly relevant today due to its adaptability and quality results.
The Basics of Silk Screen Printing
At its core, silk screen printing, also known as serigraphy, entails using a mesh screen to apply layers of ink onto a substrate. The process was refined in the early 20th century and has since been embraced by industries ranging from fashion to advertising. Modern advancements have only expanded its applications and increased its precision.
Materials Required
To embark on a silk screen printing project, several key materials are essential:
- Screens: Mesh screens, typically made of polyester, serve as the foundation upon which the design is transferred.
- Inks: Specially formulated inks ensure optimal adherence and vibrancy, especially when working with fabric.
- Squeegees: These tools help evenly distribute ink across the screen, ensuring clean imprints.
Cotton Ribbons
Cotton ribbons are particularly suitable for silk screen printing due to their durability and natural texture, which holds ink well without excessive bleeding. Their versatility allows them to be used in numerous applications, making them a popular choice for both commercial and DIY projects.
The Silk Screen Printing Process
Design Creation
Creating an effective design starts with conceptualization and moves through digital illustration. Common software tools like Adobe Illustrator and CorelDRAW offer robust features for crafting precise designs tailored for silk screen printing.
Preparing the Screen
The preparation stage begins by coating the screen with a light-sensitive emulsion. Once dry, the screen is exposed to bright light with the design placed between the screen and the light source. This exposure hardens the emulsion, leaving the areas covered by the design soft and water-soluble. A thorough wash reveals the stencil ready for printing.
Setting Up the Printing Station
Ensuring a stable setup is crucial for high-quality prints. Use frames and clamps to secure the screen, and align the work surface meticulously to prevent misalignment. Stability throughout the process guarantees consistent results.
Printing on Cotton Ribbons
Choosing the Right Inks
Selecting appropriate inks is vital. Water-based and plastisol inks are often preferred for cotton ribbons. Key factors include durability, colorfastness, and finish—water-based inks provide a softer feel while plastisols offer robustness and vivid colors.
Printing Techniques
The actual printing involves carefully placing the cotton ribbon under the prepared screen and using a squeegee to press the ink through the mesh. For even ink distribution, maintain steady pressure and motion.
Drying and Curing
Post-printing, drying and curing set the ink firmly into the ribbon fibers. Methods like air drying, heat pressing, or conveyor dryers ensure longevity and resistance to washing and wear.
Advanced Tips and Tricks
Achieving Multi-Color Designs
For more complex multi-color designs, layering techniques come into play. Each color requires a separate screen and careful registration to keep each layer perfectly aligned.
Troubleshooting Common Issues
Common challenges such as ink bleeding or uneven prints can impact quality. Ensuring proper screen tension, correct ink consistency, and maintaining a clean work environment mitigates these issues effectively.
Applications and Benefits
Branding Opportunities
Businesses leverage printed cotton ribbons for impactful branding—from gift wrapping to promotional products. Successful campaigns frequently use custom-designed ribbons to enhance brand recognition and appeal.
Craft and DIY Projects
Enthusiasts find endless creative uses for printed ribbons in personal projects, adding unique touches to handmade gifts, home decor, and accessories. Inspirational examples can drive imaginative new projects.
Sustainability and Ethics
Eco-Friendly Practices
Embracing eco-friendly practices includes choosing sustainable materials and minimizing waste. Cotton is biodegradable and renewable, making it a better choice over synthetic alternatives.
Ethical Considerations
Fair trade and ethical sourcing underscore responsible production processes, benefiting local communities and artisans involved in manufacturing materials.
Resources and Further Learning
Recommended Tools and Suppliers
Reliable suppliers like Rui Xuan offer quality materials and equipment necessary for starting your silk screen printing journey. Additionally, utilizing design software such as Adobe Suite facilitates professional-grade creations.
Learning Platforms and Communities
Multiple online platforms offer courses and tutorials in silk screen printing, fostering skill development and connecting enthusiasts within supportive networks.
Final Thoughts
The future of silk screen printing continues to evolve with emerging technologies enhancing efficiency and creativity. As the craft advances, staying innovative and experimental opens up limitless possibilities. We encourage readers to dive into their own projects and explore this compelling art form.
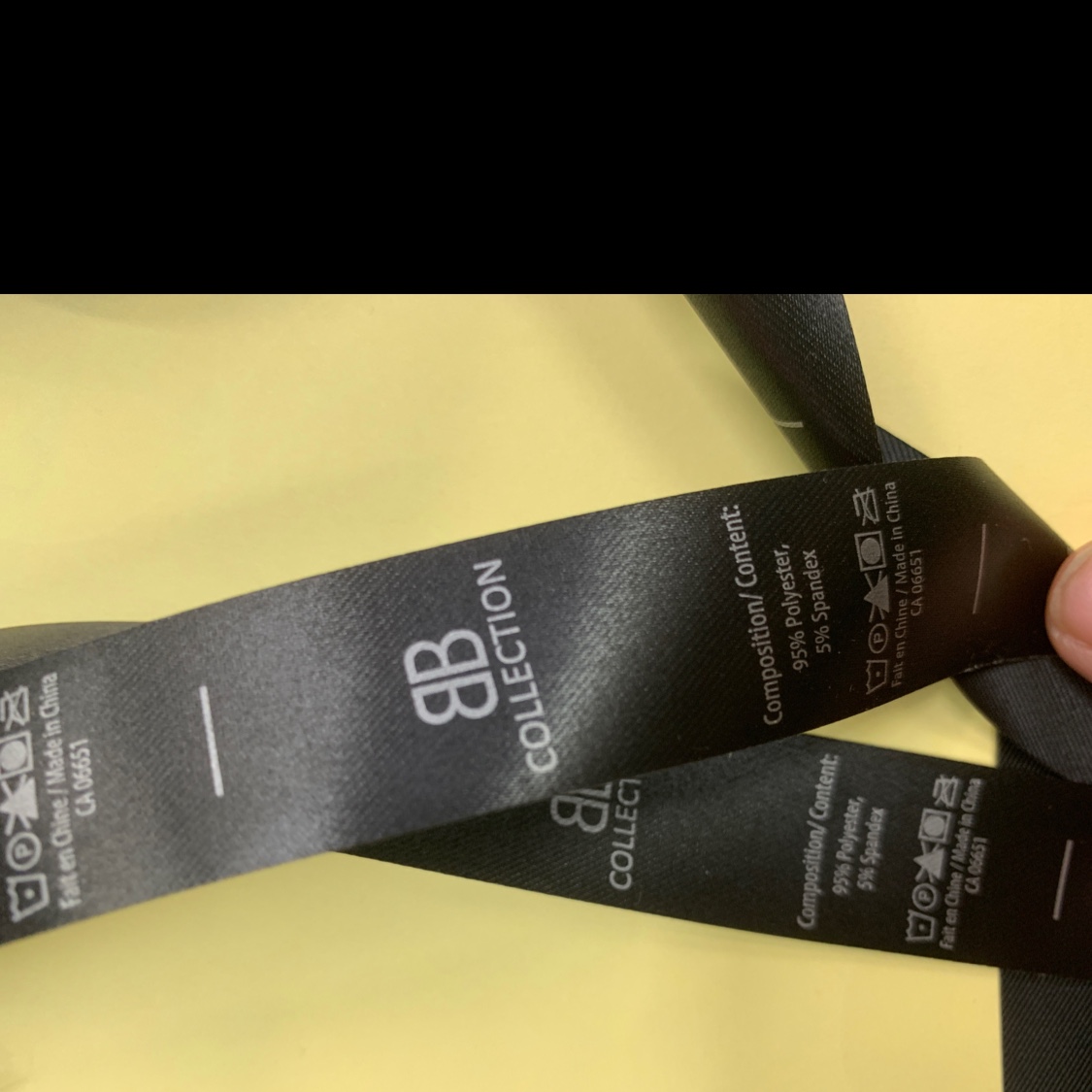